Способ обработки заготовок
Формула | Описание | Похожие патенты | МПК / Метки | Текст | Заявка | Код ссылки
Формула
СПОСОБ ОБРАБОТКИ ЗАГОТОВОК, включающий нагрев заготовок в контейнере с формообразующим элементом, имеющими коэффициент линейного расширения меньше, чем у заготовки, отличающийся тем, что, с целью обеспечения изготовления деталей сложной конфигурации, в контейнер дополнительно помещают по крайней мере одно рабочее тело, изготовленное из материала с коэффициентом линейного расширения, превышающим коэффициент линейного расширения контейнера и формообразующего элемента, а объем рабочего тела определяют по формуле
Vр.т= ,
где Vр.т - объем рабочего тела, необходимый для получения требуемой величины формообразования, мм3;
Vп - объем пустот формообразующего элемента, мм3;
Vз - объем заготовки, мм3;
t - температура нагрева, oС;з ,
p.т,
к.ф - коэффициенты линейного расширения соответственно заготовки рабочего тела и контейнера с формообразующим элементом, oС-1.
Описание
В настоящее время известен способ обработки заготовок, преимущественно из алюминиевых сплавов с одновременным формообразованием из заготовки детали, при осуществлении которого в контейнер перед нагревом вместе с заготовкой помещают формообразующий элемент, который, как и контейнер, изготавливают из материала с меньшим, чем у заготовки, коэффициентом линейного расширения.
Недостатком известного способа является то, что он позволяет производить в ходе термообработки формообразование детали в объеме, ограниченном размерами заготовки и формообразующего элемента и разностью величин коэффициентов их линейного расширения.
Целью изобретения является обеспечение возможности изготовления деталей сложной конфигурации.
Цель достигается тем, что в процессе нагрева заготовок в контейнере с формообразующим элементом, имеющим коэффициент линейного расширения меньше, чем у заготовки, в контейнер дополнительно помещают по крайней мере одно рабочее тело, изготовленное из материала с коэффициентом линейного расширения, превышающим коэффициенты линейного расширения контейнера и формообразующего элемента.
При этом объем рабочего тела определяют по формуле
Vрт=
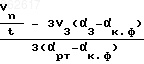
Vп - объем пустот формообразующего элемента в мм3;
Vз - объем заготовки в мм3;
t - температура нагрева при термообработке в Со;



Предложенный способ поясняется чертежом.
В контейнер 1 помещают рабочее тело 2 в виде цилиндра, а заготовку 3 и формообразующий элемент 4, который образует в месте контакта с заготовкой ряд свободных полостей 5, и закрывают крышкой (см. рисунок). При этом контейнер и формообразующий элемент изготавливают по габаритным размерам заготовки и рабочего тела, причем последнее выполняют из материала с коэффициентом линейного расширения, превышающим коэффициенты линейного расширения контейнера и формообразующего элемента.
Предварительно при заданном объеме требуемого формообразования (объем полостей 5) и температуре обработки по приведенной выше расчетной формуле определяют необходимый объем рабочего тела.
Затем контейнер с содержимым подвергают нагреву до заданной температуры обработки, при достижении которой заготовка 3 за счет расширения рабочего тела 2, создающего благодаря этому необходимое давление, подвергается пластической деформации и полностью заполняет пустоты 5 формообразующего элемента 4, принимая заданную конфигурацию. При этом одновременно происходит термическая обработка заготовки и рабочего тела и их поверхностное упрочнение.
После охлаждения контейнера и извлечения формообразованной детали процесс может быть повторен для обработки следующей заготовки.
Объем внутренней полости контейнера (V к.вн) в холодном состоянии без учета допусков на изготовление равен сумме объемов рабочего тела (Vр.т), заготовки (Vз), формообразующего элемента (Vф) и свободных полостей (Vп), заполняемых заготовкой в процессе термообработки за счет сопутствующего эффекта формообразования.
Таким образом, объем внутренней полости контейнера определяется из соотношения:
Vк.вн = Vр.т + Vз + Vф + Vп .
Толщины стенок контейнера выбирают из условия сохранения им прочности и практического отсутствия деформаций при давлении, возникающем внутри контейнера в процессе термообработки и сопутствующего ей формообразования заготовки.
Следовательно, общий объем контейнера определяют из приведенной в п. 1 формулы и прочностных требований.
Объем обрабатываемой заготовки может быть любым, а практически лимитируется конструктивными и прочностными соображениями в отношении контейнера.
Что касается величины формообразования, сопутствующего термообработке, то в известном способе он жестко лимитирован величиной объемного расширения заготовки и формообразующего элемента, а в предложенном способе теоретически не ограничен за счет введения рабочего тела любого объема. Практически же величина формообразования, сопутствующего термообработке, лимитируются только допустимыми габаритами и прочностью контейнера.
Примеры осуществления предложенного способа.
1. Из гладкой заготовки объема Vз = 86400 мм3 из алюминия марки АД-1 (


По вышеприведенной формуле определяют необходимый объем рабочего тела, выполненного, как и заготовка, из алюминия марки АД-1 (

Vрт=
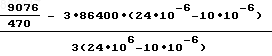
Такой объем соответствует, например, цилиндру с диаметром 40 мм длиной 300 мм.
Далее рабочее тело, заготовку и формообразующий элемент помещают в контейнер, закрывают крышкой и нагревают контейнер до температуры t = 470

За счет разности коэффициентов линейного расширения рабочего тела и контейнера с формообразующим элементом заготовка заполняет полости и при этом подвергается всестороннему сжатию давлением порядка 1000 кг/см2, за счет чего она одновременно термообрабатывается и формируется в виде заданной шестерни.
После окончания процесса один и тот же контейнер с формообразующим элементом и рабочим телом может использоваться многократно для обработки последующих аналогичных заготовок с повторением описанных операций.
Пример показывает, что введение рабочего тела позволяет значительно расширить предельные величины формообразования. При обработке предложенным способом, за счет ввода рабочего тела и варьирования его размеров позволяет изготовить термообработанную шестерню с зубом m = 3,5 мм и более, тогда как по известному способу размер зуба m = 2 мм является предельным.
2. Из гладкой заготовки объемом Vз = = 86400 мм3 из нержавеющей стали марки 0Х18Н10Т (


По формуле определяют необходимый объем рабочего тела, выполненного, как и в первом примере, из алюминия марки АД-1 (

Vрт=
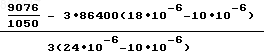
Такой объем соответствует, например, цилиндру с диаметром 40 мм и длиной 126 мм.
Данный пример наглядно показывает преимущество данного способа перед известным, где существенное формообразование при термообработке (аустенизации) нержавеющих сталей было невозможно вследствие меньшего объемного расширения этого материала, чем алюминия.
В предложенном способе введение рабочего тела, изготовленного из алюминия или любого другого материала с большим, чем у контейнера коэффициентом объемного расширения, устраняет указанный недостаток.
Очевидно, что форма рабочего тела и его размещение по отношению к заготовке могут быть иными, возможно использование одновременно не одного, а нескольких рабочих тел и т. п.
Кроме того, введение одного или нескольких рабочих тел позволяет в широких пределах варьировать размерами формообразования в процессе термообработки, т. е. обеспечивает возможности изготовления из заготовок простой формы (например, гладкого цилиндра) деталей различной конфигурации с высокой точностью - втулки, диска и т. п. сложного профиля. При этом материал заготовок (и соответственно температура термообработки) могут быть различными.
Таким образом, предлагаемый способ решает трудную техническую задачу (изготовление термообработанных деталей сложной конфигурации) простыми средствами и за одну операцию.
СПОСОБ ОБРАБОТКИ ЗАГОТОВОК, включающий нагрев заготовок в контейнере с формообразующим элементом, имеющими коэффициент линейного расширения меньше, чем у заготовки, отличающийся тем, что, с целью обеспечения изготовления деталей сложной конфигурации, в контейнер дополнительно помещают по крайней мере одно рабочее тело, изготовленное из материала с коэффициентом линейного расширения, превышающим коэффициент линейного расширения контейнера и формообразующего элемента, а объем рабочего тела определяют по формуле
Vр.т=
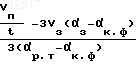
где Vр.т - объем рабочего тела, необходимый для получения требуемой величины формообразования, мм3;
Vп - объем пустот формообразующего элемента, мм3;
Vз - объем заготовки, мм3;
t - температура нагрева, oС;



Рисунки
Заявка
2850764/02, 10.12.1979
Цабунин Н. И, Гринченко А. И, Гальперин Б. Г, Пухонто И. Я
МПК / Метки
МПК: C22F 1/00
Метки: заготовок
Опубликовано: 15.05.1994
Код ссылки
<a href="https://patents.su/0-862617-sposob-obrabotki-zagotovok.html" target="_blank" rel="follow" title="База патентов СССР">Способ обработки заготовок</a>
Предыдущий патент: Импульсный генератор нейтронов
Следующий патент: Способ пакетировки длинномерных углеродных заготовок в печах графитации
Случайный патент: Механизм управления постояннозамкнутой муфтой сцепления